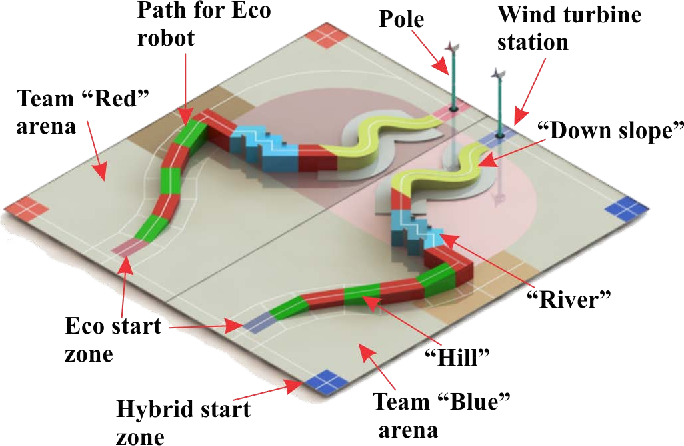
This was perhaps the most exciting theme that we had in the competition, even until today! I primarily worked on the small robot (we called it Eco-bot, shown below, top right) which was, according to competition rules, supposed to not have a driving actuator, but only a steering actuator. We settled on a wind-driven robot wherein the wind energy would be supplied by a propeller (like the ones on drones) mounted on the big robot(left, we called it the "Hybrid Robot"). The Ecobot would be driven by the Hybrid Robot via the propeller mounted on the Hybrid Robot which had a single axis of motion to accommodate for the various heights the Ecobot would be at.
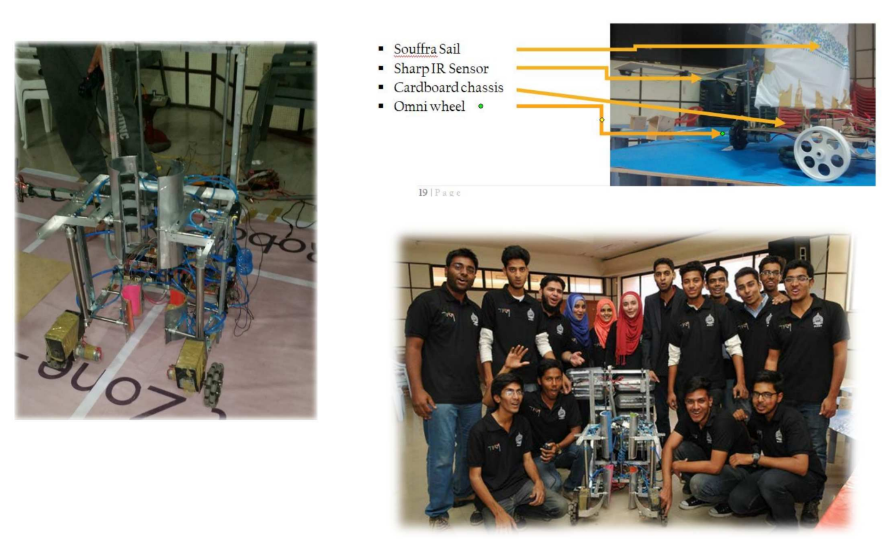
Once the Ecobot made it through the arena, the Hybrid robot would grab an item mounted on the Ecobot, called a Propeller (it wasn't an actual propeller, was just shaped like one, like the one in windmills). The Hybrid robot would then climb on top of that pole. We used pneumatic actuators on 2 levels to hold onto the pole in an alternate fashion, and bigger pneumatic actuators to provide the "upward" motion, climbing the pole like a monkey would (Look at the Hybrid robot picture to get a sense of this mechanism). We were actually able to pull off the task until here, but mounting the propeller on top of the pole with precision was a hard task, one where we faced difficulty.
My role as part of this team was a Fabricator, where I came up with prototyping ideas and used machine shop tools to either work on my own ideas or work on ideas that a team member came up with.